Fabrication
3D Printing Functional Microrobots
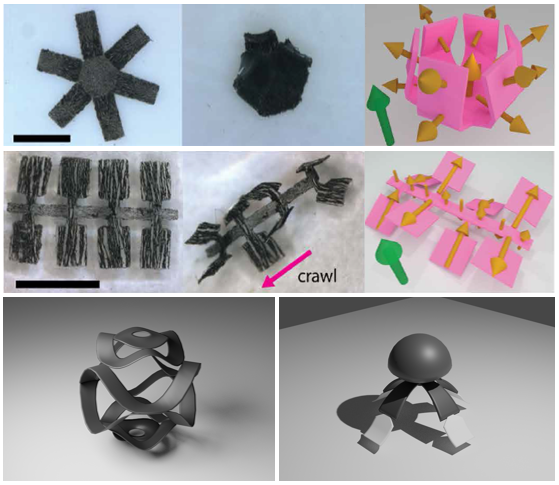
We are working on the 3D fabrication technique for magnetically-driven miniature soft robots based on Digital Light Processing (DLP). Current approach is able to fabricate single-layer 2D-folded structures. The new aim is to manufacture 3D miniature soft robots with arbitrary magnetization at each voxel, as well as create complex shape changes and locomotion mechanisms in 3D. With this method, more complex designs can be realized at high resolution on the sub-millimeter scale. New structures can be applied to perform specific tasks such as micro assembly, cargo delivery or object manipulation and become readily available for medical use.
Magneto-Acoustic Manipulation
Precise and dexterous handling of small scale objects is crucial to the development of cutting-edge products such as microsensors. Recent advancements in the field of advanced manufacturing have allowed for greater levels of assembly accuracy and precision. However, translating these advancements to the microscale remains a challenge. We aim to design an automated microrobotic factory that leverages acoustic and magnetic fields to addresses the challenges. By using the two fields, we are capable of manipulating fragile components in a sterile workspace. In the future, micro-assembly will play a crucial role in driving down the cost of manufacturing while giving researchers the tools to rapidly prototype niche products.
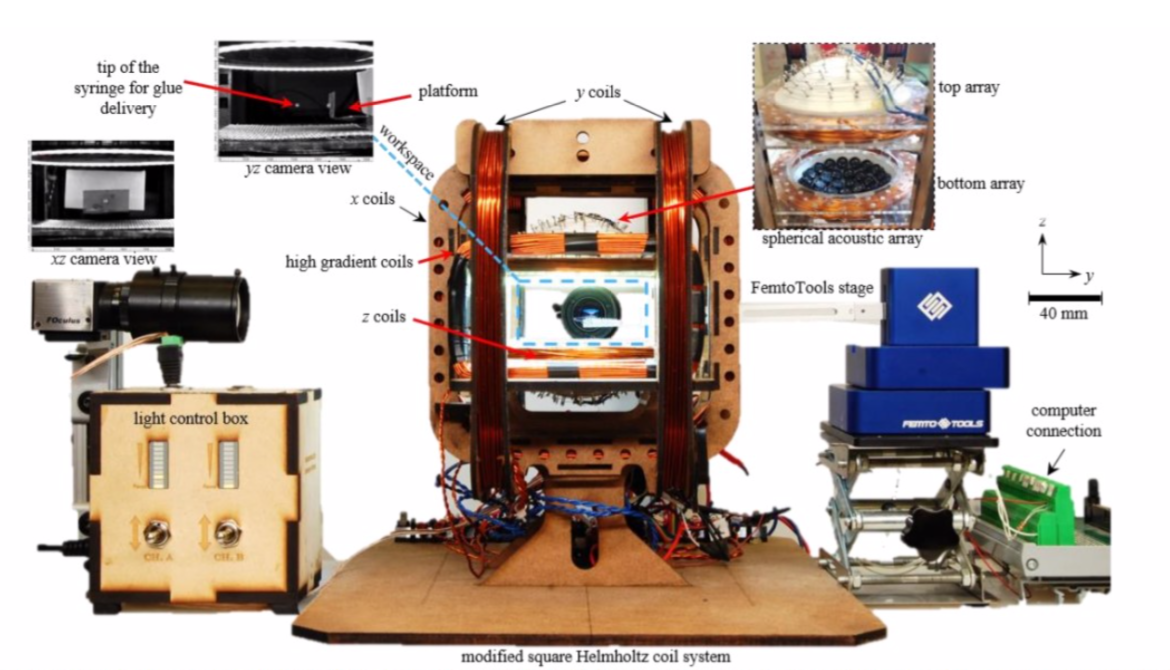
Actuation of Soft-Magnetic Microgrippers
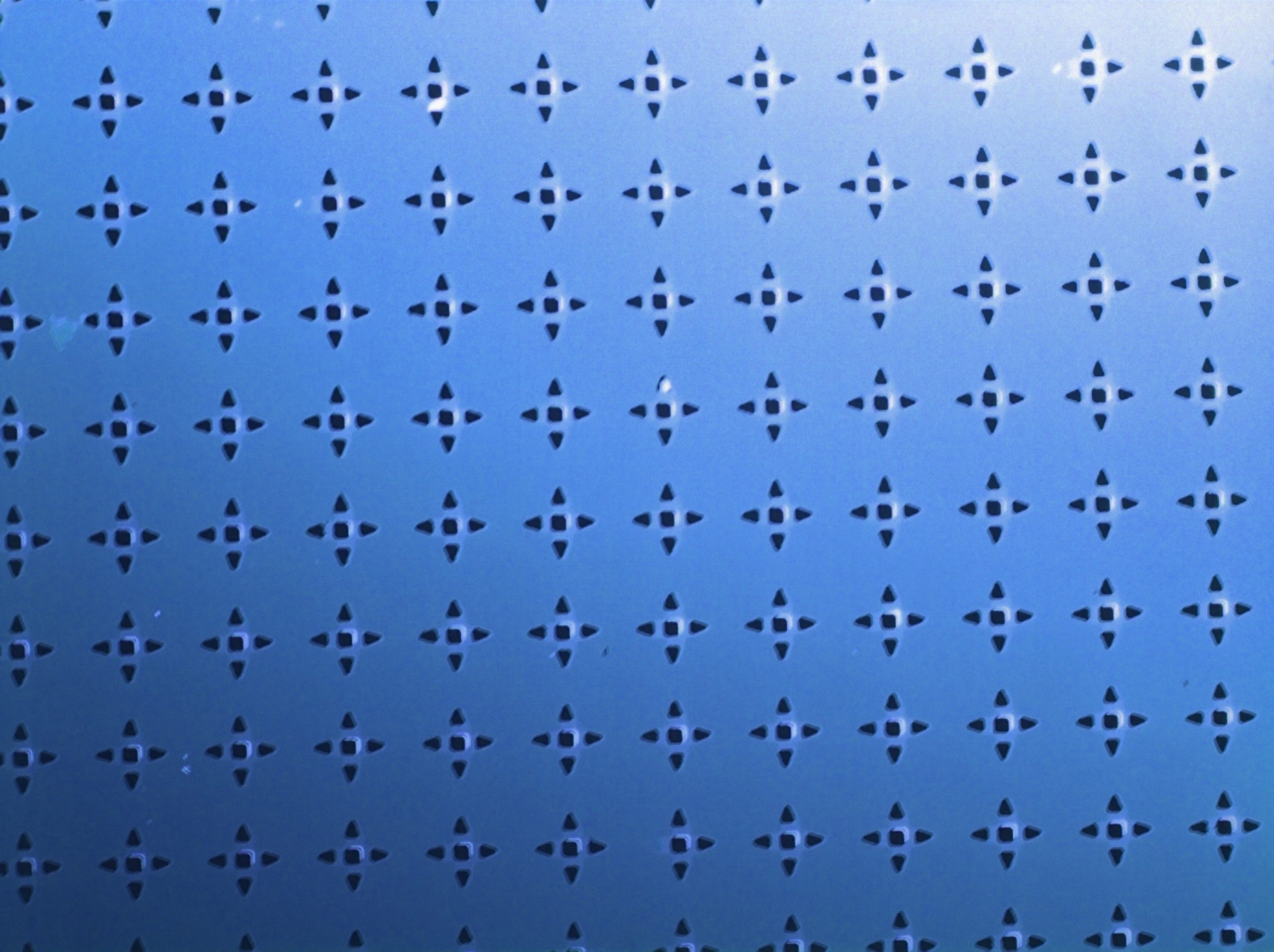
We are conducting research into actively actuating a soft-magnetic microgripper on the scale of 70µm. These microgrippers are on such a small scale that they can be used to selectively grab one particular cell of the human body. Fitted with an electrode this gripper technology could be used to one day measure the specific electrical activity of a single cell.
To properly actuate this gripper more research needs to be done, and techniques need to be developed to see the forces the gripper can achieve on this microscale. In the future, the actuation could be made addressable to be able to actuate multiple grippers simultaneously in one task.
This project is a collaboration between the Microrobotics Lab and the Gracias Lab at Johns Hopkins University.